Neue Gedanken und Möglichkeiten über Parkhausbeschichtungen einst und jetzt
- Helmut Rojek
- 29. Dez. 2018
- 6 Min. Lesezeit
Aktualisiert: 14. Sept. 2022
Liebe Leser/In !
Werte Geschäftspartner/In !
Nach mehr als 30 Jahren als Verleger, Vertriebserfahrung und auch Entwickler von Parkhausbelags-Systemen möchte ich hier meine Meinung über die Entwicklung der Garagenbeschichtungen kundtun. Meiner ganz persönlichen Meinung nach ist es allerhöchste Zeit, dass hier ein ehrlicher und offener Dialog zwischen Herstellern, Verarbeitern und Betreibern geführt wird. Insbesondere über das Thema Haltbarkeit, Unterhaltskosten und Lebensdauer von Beschichtungen. Die Erfahrungen, die Betreiber und Immobilieneigner hier machen mussten, sind in den letzten Jahren nicht die besten. Auch schaden diese Entwicklungen dem Image der Garagenbeschichtungen.

Der Erfolgskurs dieser Oberflächenbeschichtungen und die vielen Vorteile wie Bautenschutz, Farbenfröhlichkeit, Verscheißverhalten , dichte Bauwerke, könnten bei dieser Entwicklungstendenz getrübt werden.
Bilder wie diese kennen wir zur genüge:

Um hier noch etwas mehr Licht in die ganze Sache zu bringen und die Entwicklungen der letzten 30 Jahren zu verstehen, gehe ich kurz in die Historie. Anfang der 90er Jahre kam die erste Richtlinie des DAfStb heraus, welche die Parkhaussysteme in OS 8, OS 11b und OS 11a Beschichtungen gegliedert hat.
Über die OS 8 Systeme müssen wir uns nicht näher unterhalten, da diese Systeme in aller Regel auch eine gute Verschleißfestigkeit aufweisen, allerdings keine Rissüberbrückung besitzen.
Grundsätzlich geht es mir in diesem Artikel über die Lebensdauer, Verschleißbeständigkeit, Rissüberbrückungen und Dichtigkeit der Beschichtungssysteme sowie deren Schutzwirkungen für unsere Bauwerke und sowie deren Leistungsfähigkeiten .
Für die OS 11b und OS 11a Systeme war von Anfang an der Schwerpunkt auf die Rissüberbrückung gelenkt. Allerdings bot die erste Rili die Möglichkeit für den Hersteller sein System auch mit anderen Schichtdicken zu belegen, wenn der Nachweis für die Rissüberbrückung mittels Prüfzeugnis gegeben war.
Leider war auch zu dieser Zeit der eingeführte Test für die Abriebfestigkeit nicht sehr praxisnah (ist auch jetzt noch aktueller Stand) und eine Klassifizierung für die Nutzungsklassen fehlt bis heute.
Erst Anfang der 2000er Jahre, mit der Novellierung der Rili, wurde dies geändert und die Hersteller wie auch die Verarbeiter wurden in ein sehr starres Schichtdickenschema gepresst und dies vollkommen unabhängig von der Leistungsfähigkeit und Sinnhaftigkeit der einzelnen Systeme.
Der Stand der Rili Anfang der 90er hat dazu geführt, dass mein damaliger Materiallieferant dessen Generalvertretung ich war, ein System geprüft hatte mit einem mechanisch deutlich besser geeigneten Material für die sogenannte „Schwimmschicht“ (heute 1. hwO bei OS 11a oder auch Membranschicht, oder hwO bei OS 11bSystemen). Dieses damalige Material enthielt auch deutlich weniger, chemisch nicht eingebundene Weichmacher (<= 10 %). Diese Schicht war auch dünner und wies daher weniger Verwalkungen auf als die heutigen Systeme, die durch sehr hohe dz Zuschläge (Schichtdickenzuschlag) sogar noch ungünstiger gestaltet werden müssen.
In den ersten Jahren wurden vernünftigerweise aber auch viel mehr OS 11a Systeme als OS 11b Systeme eingesetzt, weil es klar war, dass die Haltbarkeit durch die härtere Verschleißschicht deutlich besser war als bei OS 11b Systemen.
Durch den hohen Wettbewerbsdruck wurde aber dann der Anteil von Weichmachern in den Stoffen deutlich erhöht (heute bis zu 20 – 30 % bei manchen Produktherstellern !!) und die mechanischen Eigenschaften verschlechtert, außerdem wurden auf Grund des massiven Wettbewerbs- und Preisdruckes und sowie der Gleichstellung in den Prüfzeugnissen (Rissüberbrückung OS11b und OS11a) für sehr viele bzw. bei fast allen Projekten OS 11b Systeme eingesetzt. Die OS 11a Systeme wurden fast nur noch maginal auf freibewitterten Flächen (Temperaturschock und Sommergewitter) verwendet.
Generell ist zu Systemen der Klasse OS 11b zu sagen, dass diese an sich nur ihre Berechtigung bei schwach befahrenen Parkflächen (z. B. Wohnungsbau) haben. Die Verschleißfestigkeitsprüfung, die die Rili bzw. DIN V 18026 vorsieht, wird zwar bestanden, hat aber wenig Aussagekraft. Ein paar Materiallieferanten haben mit ihren Beschichtungssystemen den sogenannten „Benzinger“ Test (Bilfinger, Mannheim) durchführen lassen. Hierbei wird ein PKW-Rad mit 450 kg auf die Beschichtung aufgedrückt und dann in einem Drehwinkel von 90° gedreht. Dabei wurde sehr schnell die fehlende Verschleißfestigkeit von OS 11b Systemen sichtbar.
Ein weiterer Schwachpunkt bei OS 11 Systemen sind die heutzutage eingesetzten sehr weichen Materialien. Der ursprünglich einmal verwendete Begriff „Schwimmschicht“ trifft hier an sich den Nagel auf den Kopf. Die deutlich härtere Verschleißschicht hat zwar Verbund zur 1. hwO aber aufgrund der fehlenden Festigkeiten der unteren Schicht ist die Verschleißschicht beweglich.
Das kann dann zu dem Effekt Glasplatte auf dem Sofa führen, zumal im Gesamtaufbau Verwalkungen auftreten. Die Verwalkungen können zu Mikrorissen führen, die letztlich die Zerstörung der OS 11 Beschichtung einleiten.
Viele Gespräche mit Betreibern haben mich als Verarbeiter dazu veranlasst neue, eigene Systeme zu entwickeln, in die auch neue Materialien mit bestechenden Eigenschaften eingeflossen sind. Damit die seinerzeit gültigen Bestimmungen hinsichtlich Rili DAfStb und DIN V 18026 erfüllt werden, wurden die Systeme als Abdichtung mit Spritzfolien ,Verschleißschichten ohne oder mit Quarzsand- bzw. anderen Abstreumaterialien und Deckversiegelungen mit PU- oder Epoxidharzen wie auch Polyaspartic-Harzen entwickelt.


Für diese Systeme liegt uns ein allgemein, bauaufsichtliches Prüfzeugnis nach OS 10 vor. Ein ganz wesentlicher Unterschied zu den klassischen OS 11a Systemen liegt in der 1. hwO die hierbei nämlich aus einer UREA Hybrid/ oder 100%pur Polyurea Spritzfolie besteht. Die Shore Härte hierbei liegt bei ca. Shore A 88 -92 (entspricht etwa Shore D 40-45), die Shore Härte bei klassischen handverarbeiteten Produkten liegt bei ca. Shore A 65- 67 (entspricht etwa Shore D 19). Außerdem enthält eine Polyurea-Spritzfolie keine Weichmacher und dies noch bei einem höheren Niveau der Rissüberbrückung. Die mechanische Festigkeit einer derartigen Polyurea-Hybride oder 100%pur Polyurea-Spritzfolien ist wesentlich besser als die klassischen handverarbeitbaren Materialien.


Bei abgestreuten OS10 Systemen aus unserer Flexiskin-Linie besteht die Verschleißschicht aus einem reinen Polyurethan mit einer Shore D Härte von ca. 73. Die Versiegelung kann entweder mit einem Epoxidharz oder einer Versiegelung auf Polyasparticbasis erfolgen. Polyaspartic-Systeme haben
die Vorteile absolut UV-stabil, farbtonbeständig, sehr gut reinigbar und frühwasserbeständig zu sein.

Mit diesem System haben wir die Abdichtung über einem Parkdeck in einer Müllverbrennungsanlage in Wien hergestellt. Die Beschichtung liegt jetzt seit 3 Jahren. Der Untergrund ist Beton und der Verkehr ist intensiver schwerer LKW-Verkehr, die Fahrzeuge reversieren, bremsen und tragen viel Schmutz ein. Auf dieser Fläche fahren mind. 1/3 aller Müllautos Wiens darüber. Bis auf wenige Stellen von massiven mechanischen Zerstörungen durch das Abstellen von Containern und Anfahrschäden liegt dieser Belag bis heute einwandfrei. Eine bessere Verschleißprüfung gibt es an sich nicht mehr.

Noch revolutionärer bzw. fortschrittlicher ist das System welches wir vor 3-4 Jahren für einen großen Parkhausbetreiber für den österreichischen Markt entwickelt haben. Es wird in unter dem Namen Flexiskin Grip vertrieben.
Es besteht aus einer reinen UREA Spritzfolie inkl. einer Verschleißschicht die ebenfalls aus Polyurea hergestellt wird und einer Signalschicht als Deckbeschichtung auf Basis von Polyaspartic und speziellen Zusätzen um die Rutschfestigkeit zu erreichen.

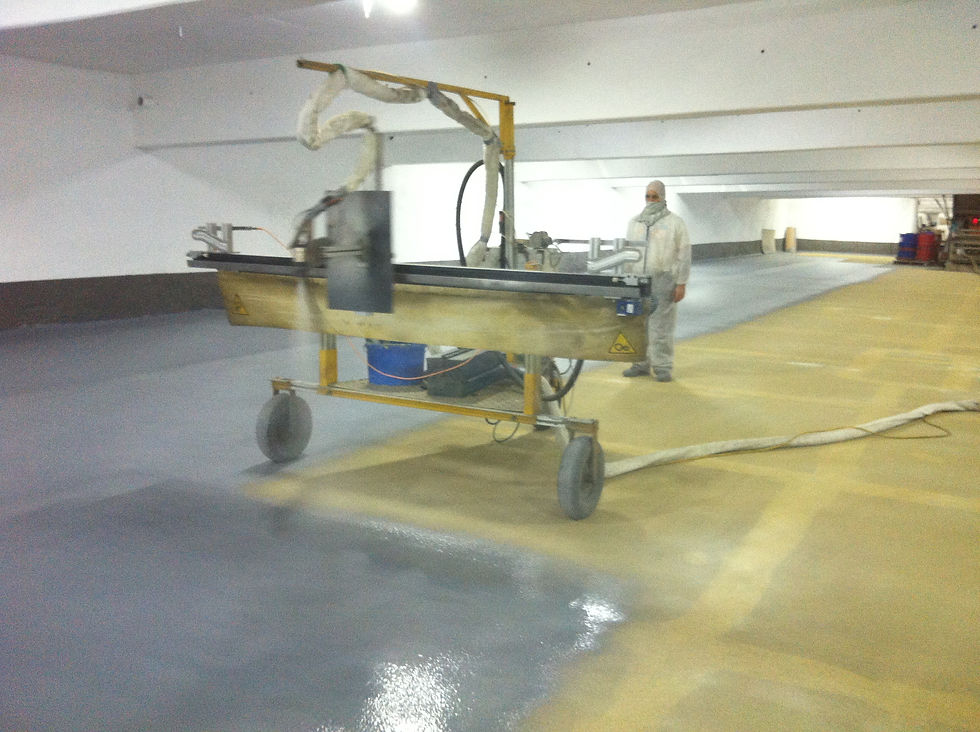
Diese Beschichtung kann und wird mit einer speziellen Robot-Technologie verlegt um sicher zu stellen, dass über die
gesamte Fläche eine einheitliche Schichtstärke gewährleistet wird.

Die Sprüh- bzw. elektronisch überwachten druck- und mengengesteuerten Dosieranlagen garantieren absolute Mischgenauigkeit. Flexiskin Grip wurde im Vergleich zu klassischen Systemen unabhängig vom Bauherren auf Verschleiß nach Böhme geprüft. Das Ergebnis war, dass dieses System um den Faktor 3 – 4 weniger Verschleiß aufzeigt. Außerdem erfüllt Flexiskin Grip die Anforderung der Nachhaltigkeit, da nur noch im geringsten Masse Quarzsand vor Ort in die Grundierungen eingesetzt wird (Schonung von Ressourcen). Von den hervorragenden Rissüberbrückungseigenschaften ganz zu schweigen.
Dieses System ist außerdem extrem schnell, und eignet sich bei Teilsanierung zb. Rampen und den Einfahrtsbereichen bei Garagen ganz besonders.
Als Beispiel:
Bei einer Tiefgarage in Italien haben wir ca. 200 m² Rampenfläche in 12 Stunden mit diesem System ertüchtigt. Beginn der Untergrundvorbereitung ca. 20.00 Uhr, Abschluss der Beschichtungsarbeiten gegen 04.15 und erste Überfahrt wieder um 08.00.
So gut wie keine Geruchsbelästigung, Frühwasserbeständigkeit kein Thema. Dieses System zeigt eine ausgesprochen hohe Verschleißfestigkeit, sollte hier aber trotzdem einmal die Überarbeitung der Signalschicht notwendig werden, so ist dies über Nacht möglich, ohne Sperrzeiten für die Flächen und damit kein Ausfall der Einnahmen.


Bei dem System Flexiskin Grip als auch bei anderen OS10 Spritzfolien - Belägen mit Polyaspartic- oder Epoxidharzversiegelungen ist es möglich tatsächlich eine wasserdichte Wanne herzustellen. Die Spritzfolien der beiden Systeme weisen auch eine sehr geringe Wasseraufnahme < 1,5% auf, die es ermöglichen alle Rinnen, Entwässerungen und sonstige abdichtende Details sicher auszuführen.
Dies ist mit herkömmlichen System nur mit großen Mühen erreichbar und wird in der Praxis nicht durchgeführt. In der österreichischen Richtlinie für Garagen und Parkdecks ist jetzt schon explizit angeführt, dass die Hochzüge nur mehr mit der abgesandeten Grundierung versiegelt werden.
Mittlerweile wurden von dem System Flexiskin Grip mehr als 250.000 m2 zur vollster Zufriedenheit der Bauherren verlegt.

Zwischenzeitlich haben wir Versuche mit brandgeprüften 100%pur Polyureas mit Shore A >100 = Shore D 50 ohne Kopfversiegelungen im laufen. Die Testflächen weisen hervorragende Ergebnisse auf. Die Flächen bewähren sich bestens und werden auch wirtschaftlich sehr positiv beurteilt. Wie Sie sehen ist sehr viel mehr möglich als die Richtlinie DAfStb in Deutschland sowie die Richtlinie Garagen und Parkdecks Österreich überhaupt zulässt. Dies hat uns auch veranlasst in der neuen Richtlinie "Spritzfolien" auf dieses Thema besonders einzugehen und diese Systeme der Öffentlichkeit präsent zu machen. Mittlerweile werden von großen Systemherstellen ebenfalls schon ähnliche Technologien angeboten was der Beweis ist, dass wir als Flexiskin doch Vorreiter und Umdenker in der Beschichtungstechnologie für Parkgaragen sind.

Als Schlusswort möchte ich anmerken:"Nur wer bereit ist, Herkömmliches zu verändern und Gewohntes zu erneuern, wird Erfolg haben. Auch bei den Garagenbeschichtungen ist ein Umdenken notwendig.
„ Eine wirklich gute Idee erkennt man daran, dass ihre Verwirklichung von vornherein ausgeschlossen erschien. “Albert Einstein

Sollte ich Ihr Interesse geweckt haben kontaktieren Sie mich.
Helmut Rojek
Geschäftsführender Gesellschafter der Flexiskin GmbH und Rojek GmbH
www.flexiskin.at oder www.rojek.at
Mail: helmut@rojek.at oder rojek@flexiskin.at
Comments